Stock level management best practice
An empty shelf where your product ought to be inevitably means lost sales. Most customers will opt for a competitor’s product from the next aisle, go elsewhere or simply abandon the purchase. Research has shown that the potential revenue gain from on-shelf availability optimisation can be as much as 29%. This white paper describes the context in which on-the-shelf availability is becoming increasingly important for sport and leisure brands, and highlights key areas where improvements can be made.
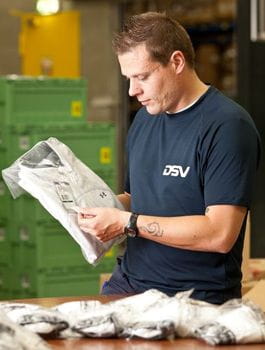
The days of two fashion seasons a year are over. Even luxury brands such as Prada and Louis Vuitton are switching to four to six collections a year instead of two. Increased price consciousness among consumers has also made them less loyal to brands. This is especially true for the less fashionable, more practical sports and leisure brands. As a result it is getting more and more difficult to achieve on-the-shelf availability for the entire product range. Another consequence of out-of-stock incidents is customer frustration, which can lead to further detachment from the brand.
On top of it all, own label brands have been gaining ground. According to Rabobank, a Dutch financial institution, market share for retailers’ own label brands has increased rapidly in recent years, most notably in the UK, Spain, Germany, Italy and the Netherlands. Own label brands are estimated to have achieved at least 40% market share in five countries. In the UK and Switzerland, they account for one of every two products sold. In this context, uninterrupted availability of a brand’s product in stores has become vital for survival.
The sports and leisure industry is characterised by high seasonality and fierce competition for retail space. The brand owner’s or distributor’s challenge is getting the products to the shelves of the retailers and then making sure stocks don’t run out. The critical success factors in this challenge are:
- Demand forecasting
- Size of product range
- Order and delivery process
- Products display size
- Stock list accuracy
Demand forecasting
Accurate demand forecasting is the starting point for planning all supply chain operations. Traditionally, forecasts have been based on historical sales data. Yet past sales volumes do not necessarily predict future customer demand as, inter alia, it does not always take out-of-stock situations into account. For new products, an accurate forecast of sales volumes ultimately depends on the commitment of the retailers. Depending on the quality of the relationship, the retailer may be overly conservative in his estimates if the forecast commits him to a minimum quantity. It is better for a retailer to be motivated to give an ambitious forecast by not committing to any minimum contractual obligations.
Size of product range
A disciplined approach to optimising the product range and relentless scrutiny of products outside the core portfolio is key to maintaining high product availability. It is natural to have tension between “building the brand” by expanding the range of products on the one hand, and keeping the number of products manageable in order to maintain high availability on the other. But companies need to foster a mindset where optimising the current portfolio is second nature for its employees.
Relentless scrutiny on products outside the core portfolio
Order and delivery process
The use of planning sheets for the end-to-end production process, and a timely order process, are obviously the basis for getting your goods onto the shelves on time. A stable relationship with one logistics services provider, or a limited number of them, can help to ensure capacity in the container and provide a reliable service for emergency air freight for sizes out of stock. What’s more, the tipping point for the most economical shipping costs of an LCL (less than container load) compared to an FCL (full container load) is often lower than you would expect. In combination with volume discounts at the manufacturer, this makes larger volumes extra attractive from a cost perspective. The order and delivery process is often characterised by huge volume/cost breaks. It is important to calculate the total landed costs of a wide range of scenarios and the advantages associated with each supply model.
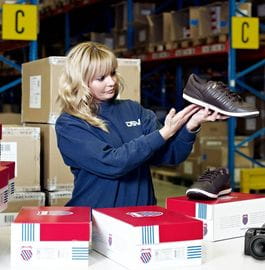
Product display size
The larger the retail space per product, the larger the buffer to prevent out of stock situations. The reality however is fierce competition for product display area, often side-by-side with your direct competitors. A larger area in the store also often means more opportunities to exchange slow-moving products that are out of stock with fast-moving stock. Retailers that provide brands with space for a complete concept will get more attention from those brands, who will want to make sure their product range is optimised for the store and prevent the popular style/size/colour combinations from going out of stock.
Stock list accuracy
The accuracy of stock forecasts and availability is greatly improved by integrating specialised warehouse management systems into the planning software. Having up-to-date and sufficiently detailed information about quantities in stock and on order is crucial for a smooth supply chain. Radio frequency scanning for each stock movement and real-time availability of the data supports decision-making and ultimately leads to increased availability of the products on the shelves.
Cases
We will discuss two examples of sports and leisure goods brand owners and how they have succeeded in reducing the number of out-of-stock incidents. Although their situations are different, they give useful insights into different strategies for optimising on-the-shelf availability. We will also look at SportMonitor, a supplier of retail benchmark software.
Rucanor: Get the basics right
This iconic sports brand originating in The Netherlands in 1956 is best known for its sports peripherals such as fitness equipment, sports bandages and protection products, swimming/diving products, boxing gear, shoes and clothing. During its heyday in the 1980s, the company developed a broad product range which, in addition to its core peripherals, included lines of sports fashion items such as T-shirts, jackets, training suits and bathing suits. Due to the changing economic climate and fierce competition, the company struggled to keep up sales volumes for its entire product range. In March 2013, the brand was re-launched by Sport Services Europe. The new exclusive licence holder of the Rucanor brand made drastic changes to the product portfolio. Most of its seasonal and fashionable product lines were stopped and it adopted a strategic focus on its core products. Currently the company is consistently expanding and deepening its 'never out of stock' portfolio including swimming and running gear, protective pads, martial arts equipment, sports apparel, etc. The team of merchandisers as well as its network of distributors in Europe are succeeding in optimising on-shelf availability. As a large part of the products are now produced to stock, IT connections with the major retailers and distributors allow for timely replenishments. A clear focus on its core products has enabled Rucanor to achieve the economies of scale required to be competitive in terms of price and customer service. “Our new “Get the basics right” slogan reflects this successful strategy very well” says Martijn Nelissen, the owner of Rucanor.
Oakley: Better sales forecasts
California-based Oakley manufactures performance sports equipment and lifestyle items including sunglasses, sports visors, ski and snowboard goggles, watches, apparel, backpacks, shoes and other accessories. From their European Sales and Marketing department in Zurich and their European Distribution Centre in the Netherlands, they have seen steady growth in their European business. Whereas previously, order quantities for next season’s stock were based on rough estimates, they have started increasing their reliance on sales forecasts by their retailers. Their approach towards their retail network focuses on growing with key accounts in combination with a network of own stores, store-in-store concepts and consignment stock. This more stringent forecast process has made recent seasons’ collections more focused, with higher volumes of lower numbers of products. As a result of this approach, the amount of end-of-line stock sold through factory outlets has drastically decreased. From a supply chain perspective, the traditional two seasons are increasingly overlapping. “The challenge in the warehouse environment is that the traditional two-week season changeover of stock locations is disappearing”, says Harold Heutink, Logistics Manager of the Oakley European Distribution Centre (EDC). Harold is responsible for all logistics activities in Oakley’s EDC and distribution of products to Europe, Middle East and Africa. Besides the outbound distribution, the EDC also manages all reverse logistics such as product returns and warranty claims.
SportMonitor: Big data at work
The philosophy of SportMonitor, a supplier of retail benchmark software, is that sales optimisation is based on data sharing between brands/distributors and retailers. The dreaded “…but I can order it for you” when a size is not in stock nowadays almost inevitably leads to a customer buying a product online. SportMonitor provides retailers and brands with sales data. The tool is directly linked to the cash registers of over 125 sports retailers and provides insights into sales volumes and seasonality depending on weather, holidays and other variables. “Having a reliable sales forecast taking influencing factors into account greatly improves on- shelf availability”, says Friso Berghuis from SportMonitor. Perry van Stuivenberg from DAKA, a company using SportMonitor for their own sports retail stores, agrees. “The more a retailer and a brand can optimise their sales forecast by sharing data, the more confident the retailer will be about placing ambitious orders,” explains Perry. “IT connections between brands and retailers are nothing new but proactive consolidation and subsequent reporting of sales and benchmark data from both large and small stores opens up an array of opportunities for maximising the availability of the right product, at the right place, at the right time”, concludes Friso.
About the experts
Simon Kos has been active in the apparel industry for over 15 years in production planning and execution. He specializes in effective sourcing and supplier management in China and India as well as quality control and supply chain. He started on the retail side at Macy’s in the US and subsequently managed the production of apparel collections of Bjorn Borg, McGregor, Euretco (ELC) and Royal Bamboo. In 2009 Simon founded Real Apparel Management B.V. advising brand owners on topics including sourcing, production and supply chain.
Any questions?
Our experts are ready to help. Get in touch and we'll find the solution you need.
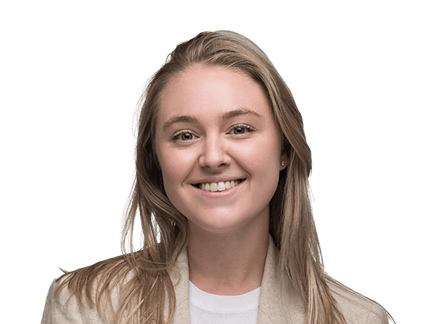