Optimización de logística automotriz
¿Se puede negociar el ahorro de costos logísticos?
No cabe duda de que tal estrategia supone ciertos beneficios a corto plazo, pero a medio y largo plazo, existen límites sobre qué tipo de reducción de costos se pueden lograr presionando a los proveedores. La alegría inicial de haber conseguido una reducción de costos se puede convertir rápidamente en una decepción cuando surgen costos fuera del control del proveedor, o de su propio control, todo ello comienzan a dejar un regusto amargo. Estos incrementos pueden incluir costos de combustible, originarse por desequilibrios en la capacidad del mercado o simplemente ser el resultado de una mayor complejidad de su logística.
Muy pocos negarían que la optimización es el camino a seguir... Pero, ¿cuál es la forma correcta de optimizar?
Proveedor de 1er Orden (Tier 1) ya está muy optimizado
Esto lleva a los Proveedores de 1er Orden a situar sus fábricas cerca de las plantas de producción, para que los componentes puedan entregarse casi directamente a la cadena de ensamble para una fabricación en cadena just in-time. Muchos de esos componentes son relativamente grandes y difíciles de almacenar, de modo que es mucho más sencillo fabricarlos bajo demanda que ocupar un espacio en el almacén con los consiguientes movimientos logísticos adicionales de entrada/salida.
Cuando se trata de proveedores que entregan a la fábrica de Proveedor de 1er Orden (conocidos como Proveedores de 2do Orden), es mucho más probable que estén situados en otro lugar, incluso en otro país. Los costes de transporte y logística para la parte de Proveedores de 2do Orden 🠖 Proveedores de 1er Orden Nivel 1 de la cadena de suministro son, por tanto, más complejos.
Informe de Transport Intelligence
- Gastos de aprovisionamiento para los fabricantes de vehículos (OEM): Gastos en la logística de recepción y dentro de la planta de ensamble del OEM. Esta actividad suele consistir en la recogida de las mercancías de los proveedores siguiendo distintos métodos.
- Gastos de aprovisionamiento para los proveedores de los fabricantes de vehículos (Proveedor de 1er y de 2do Orden): Logística de recepción de materiales y en torno a las instalaciones de todos los proveedores (se trata de un costo oculto para los OEM incluido en el precio de los componentes)
- Vehículo terminado / Salida: Operaciones con vehículos terminados de los fabricantes de vehículos, incluyendo transporte, manipulación / inspección previa a la entrega (PDI) y gestión de inventario. El servicio posventa incluye la distribución de piezas de repuesto.
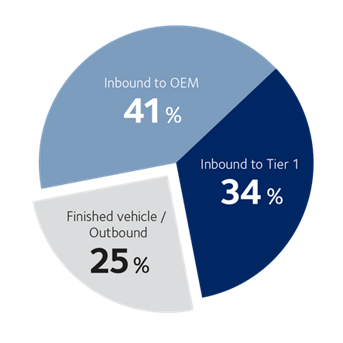
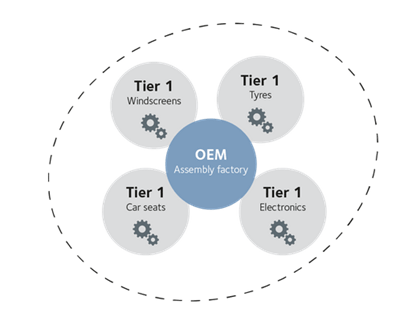
Ampliación de la optimización al Proveedor deTier 2
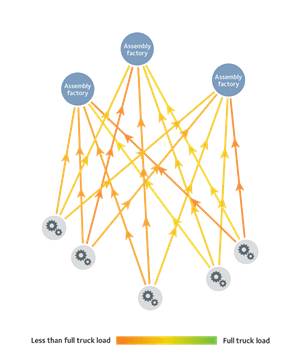
Piel
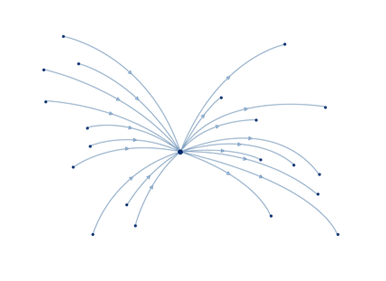
Análogo al modelo aéreo de red radial:
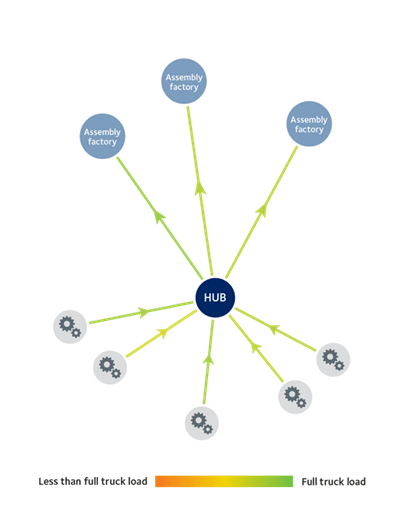
Centro de distribución
El resultado se traduce en un ahorro notable. También resulta más sencillo coordinar entregas just-in-time. Por supuesto, la ubicación geográfica del centro de distribución es importante para no dedicar tiempo innecesario a largos tiempos de tránsito. Contar con un centro de distribución en la cadena prolonga los tiempos de tránsito, aunque ello no debería suponer un problema una vez que la cadena está en funcionamiento y que se calculan los tiempos de tránsito dentro de una planificación puntual. Como resultado, la cadena de suministro es más sencilla y más eficiente.
Milk runs
Las rutas de reparto optimizan la recogida local y la idea procede de los camiones de leche que visitan varias granjas para recoger la leche y solo regresan al almacén una vez la cisterna de lecha esté llena y ya no hay más leche para recoger en la zona.
Este tipo de optimización supone numerosas ventajas: al llenar los camiones y hacer menos recogidas parciales, el número de movimientos de los camiones es menor, logrando un uso más eficiente de la capacidad del muelle, los camiones y los conductores, el combustible, los peajes y muchos otros aspectos, en particular la reducción de las emisiones de CO2.
Conclusiones
Gran parte de los costos de los componentes en niveles inferiores de la cadena de suministro incluyen costos ocultos que son consecuencia de cadenas de suministro no optimizadas.
Un análisis cuidadoso más allá del nivel de los Proveedores de 1er y 2do Orden puede suponer un ahorro notable reduciendo el costo que se produce al enviar demasiadas cargas parciales en lugar de cargas completas.
Acerca del autor
¿Alguna pregunta?
Nuestros expertos están disponibles para ayudarte. Ponte en contacto y encontraremos la solución que necesitas.
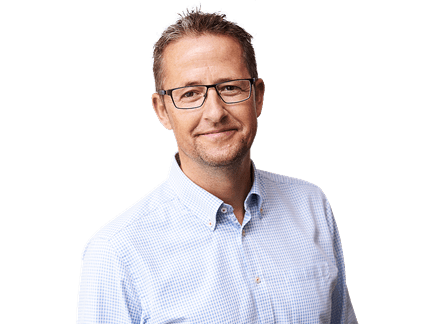