Optimaliser forsyningskjeden i bilindustrien
Kan du bare forhandle innkommende kostnadsbesparelser?
Å redusere kostnadene i forsyningskjeden starter nesten alltid med å ønske å reforhandle kontrakter med tredjeparts logistikkleverandører. Neste trinn er anbudsforespørsler for å sammenligne priser mellom leverandører.
Denne strategien kan gi fordeler på kort sikt, men det er grenser for hvilke besparelser som kan oppnås ved å legge press på leverandører på mellomlang til lang sikt.
Sødme av en innledende kostnadsreduksjon kan raskt bli forsuret når kostnadene øker utenfor leverandørens - eller din - kontroll begynner å etterlate en bitter ettersmak. Slike økninger kan inkludere drivstoffkostnader, komme fra ubalanser i markedskapasiteten eller bare være et resultat av økt kompleksitet i logistikken.
Få er uenige i at optimalisering er veien videre - men hva er den optimale måten å optimalisere på?
Tier 1 stort sett allerede optimalisert
OEM-er - produsenter av originalt utstyr: selskapene som har navnet sitt på de ferdige kjøretøyene har blitt veldig dyktige til å optimalisere innkommende logistikk. I de fleste tilfeller arrangerer OEM-forsendelse fra komponentfabrikken (kalt en Tier 1-leverandør) til bilmonteringsanlegget.
Dette har ført til at Tier 1-leverandører har plassert fabrikkene sine nær monteringsanleggene, slik at komponenter kan leveres nesten direkte til samlebåndet for just-in-time produksjon. Mange slike komponenter er relativt store og vanskelige å lagre, så det er mye lettere å produsere dem i henhold til etterspørsel, i stedet for å ta dem lagerplass med påfølgende ekstra inn / ut-logistikkbevegelser.
Når det gjelder leverandører til Tier 1-fabrikken (kjent som Tier 2-leverandører), er det langt mer sannsynlig at disse leverandørene er lokalisert andre steder - selv i et annet land. The transport costs and logistics for the Tier 2 --> Tier 1 part of the supply chain are therefore more complex.
Transport etterretningsrapport
I 2014 publiserte Transport Intelligence en rapport om Automotive Logistics basert på arbeid fra International Car Distribution Program (ICDP). Rapporten identifiserte tre kategorier av logistikkostnader og angir forbruket til alle europeiske bilprodusenter:
- Inngående til produksjon for bilprodusenter (OEM): Bruk av logistikk til og innenfor OEMs monteringsanlegg. Denne aktiviteten samler vanligvis varer fra leverandører gjennom forskjellige metoder.
- Inngående til produksjon for bilprodusentens leverandører (Tier1 / Tier2): Logistikk av materialer til og rundt alle leverandørers fasiliteter (dette er en skjult kostnad for OEM-er inkludert i komponentprisen).
- Ferdig kjøretøy / utgående: Bilprodusentens ferdige kjøretøyoperasjoner inkludert transport, håndtering / PDI (forhåndslevering inspeksjon) og lagerstyring. Ettermarkedet inkluderer distribusjon av reservedeler.
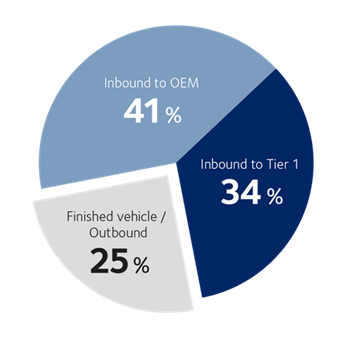
Tallene viser at kostnaden for Inbound to OEM og Inbound to Tier 1/2 logistics kombinert utgjør 75% av den totale logistikkostnaden.
Det er derfor forsvarlig å se på besparelsene som kan oppnås i disse kategoriene til sammen.
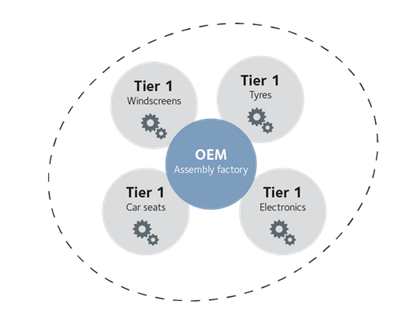
Utvide optimaliseringen til nivå 2
For å illustrere dette, la oss se på en av de mange artiklene som leveres til en OEM av en Tier 1-leverandør - bilseter.
Bilseteleverandøren er kontrakt på å levere seter til OEMs monteringsfabrikk.
I likhet med andre leverandører ligger fabrikken svært nær OEMs monteringsanlegg, faktisk så nær at de ofte er innenfor samme forbindelse, og transport kan derfor trolig oppnås med gaffeltrucker.
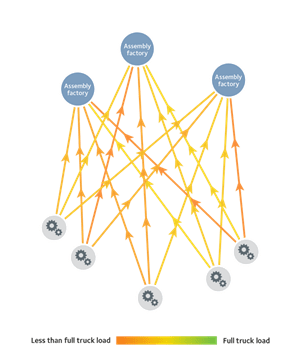
Lær
Det er umulig for alle fabrikkene i en forsyningskjede å være nær hverandre - spesielt når man vurderer råvarer som kan komme fra landbruket eller til og med nedenfra havbunnen når det gjelder olje som brukes til å lage plast. For eksempel produseres aluminium ved energiintensiv smelting som må foregå nær pålitelige, billige strømforsyninger.
Et av materialene som brukes til å lage bilseter er lær.
Hver skinnleverandør leverer faktisk mer enn en bilsetefabrikk og nesten helt sikkert mer enn en OEM - diagrammet nedenfor viser disse strømningene i forenklet form, og det faktum at ikke alle forsendelser er full last. Hver leverandør har derfor flere lastebiler i uken som samler inn dellast (LTL - “mindre enn full last av last”) og kjører dem til hver fabrikk de leverer.
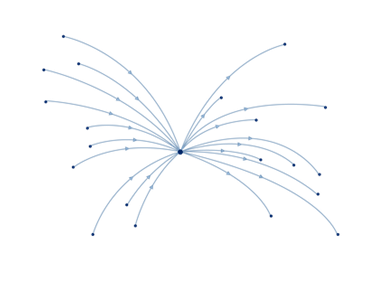
Analogt med fly-modell med nav og eiker:
Hvis du vil fly fra en stor flyplass til en annen, er sjansen stor for at du kan finne et utvalg av direkteflyvninger direkte.
Men når det ikke er tilstrekkelig etterspørsel etter seter mellom små byer, er det sannsynlig at du må koble til via en hub-flyplass.
Siden det ikke er mulig å fylle et helt fly på en direkte rute flere ganger om dagen, kan et flyselskap kjøre en mer effektiv operasjon ved å fly større fly fra de små byene til en større knutepunktflyplass. På navet overfører passasjerer til andre fly som tar dem til deres endelige destinasjon.
Det er akkurat denne nav- og eikemodellen som kan brukes for å optimalisere en forsyningskjede.
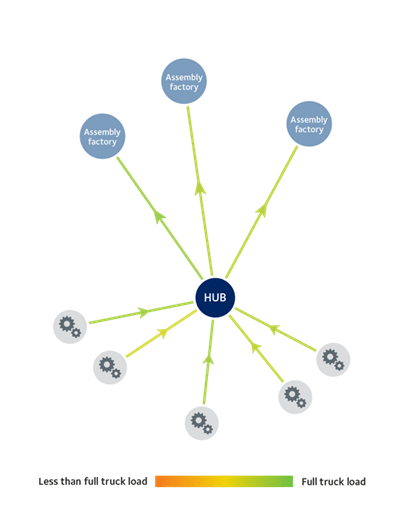
Distribusjonssenter
Ved å plassere et distribusjonssenter på et passende sted, kan forsyningskjeden bli mye mer effektiv ved å redusere mindre enn full last av last og direkte, direkte stopp. Denne konsolidering og justering av strømningene reduserer antall lastebiler som trengs. Videre kan distribusjonssentralen være en tverrdokk hvis input og output kan koordineres spesielt godt, og dermed unngå behovet for lagring.
Resultatet er betydelige besparelser. Det er også mye enklere å koordinere just-in-time leveranser. Selvfølgelig er distribusjonssenterets geografiske beliggenhet viktig for ikke å ha unødvendig lange transittider. Å ha et distribusjonssenter i kjeden forlenger ikke de totale transittidene, men dette er ikke et problem når kjeden er i gang og transittidene er beregnet inn i just-in-time planleggingen. Forsyningskjeden er enklere og mer effektiv som et resultat.
Melkekjøring
Denne optimaliseringsmetoden med et distribusjonssenter trenger ikke være frittstående. Det kan selvfølgelig kombineres med andre metoder som det som er kjent som melkekjøring.
Melkekjøringen optimaliserer lokal innsamling og er oppkalt etter melketankskipene som besøker flere melkeprodusenter for å samle melk, og bare returnerer til depotet når tankbilen er full eller det ikke er mer melk i området å samle på.
Denne typen optimalisering gir mange fordeler: ved å frakte flere fulloads og færre partilast, blir antall lastebilbevegelser lavere, noe som gir mer effektiv bruk av dock kapasitet, lastebiler og sjåfører, drivstoff, bompenger og mange andre aspekter - ikke minst redusert CO2-utslipp.
Konklusjoner
Ved å undersøke ikke bare delene av bilforsyningskjeden ved siden av den siste monteringsfasen (Tier 1), er det omfattende transport- og logistikkbesparelser å gjøre. Transportkostnader for inngående til Tier 1 og Tier 2 utgjør kostnader tre ganger høyere enn for utgående transport fra sluttmontering til sluttkunder.
Mye av kostnadene for komponenter i lavere forsyningskjedetrinn inkluderer skjulte kostnader som er en konsekvens av at forsyningskjeder ikke er optimalisert.
En nøye analyse av mer enn bare det øverste nivået i forsyningskjeden kan føre til store besparelser ved å redusere svinnet som skyldes frakt for mange partilast i stedet for fulloads.
Om forfatteren
Ronald Poort er DSVs kommersielle direktør for Solutions.
Noen spørsmål?
Våre eksperter er klare til å hjelpe. Ta kontakt så finner vi løsningen for deg.
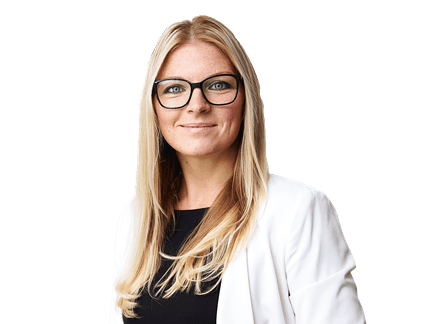